Guide
A framework for manufacturers to operate amid health risks
Companies that demonstrate readiness, innovation, and adaptability will not only survive but thrive in a post-crisis economy
May 08, 2020
The COVID-19 pandemic has touched every corner of every industry, creating short-term upheaval for millions of Americans. But even when the curve begins to flatten, and even if and when a vaccine becomes available, the effects of the crisis will last longer than anyone could have initially imagined.
That’s part of the reason why manufacturers must consider the impact of operating with immediate and longer-term extensive health and safety measures required to protect both employees and customers. This is not an easy task and will impact productivity, service levels, operating costs, employee engagement, and customer experience. But waiting or doing nothing is not an option.
To operate and thrive, companies must create a safe work environment while also innovating and adapting ways of working to preserve productivity and service while also managing costs. Companies that demonstrate readiness, innovation, and adaptability will not only survive but thrive in a post-crisis economy.
Businesses need to address employee and customer health and safety or risk significant business disruption
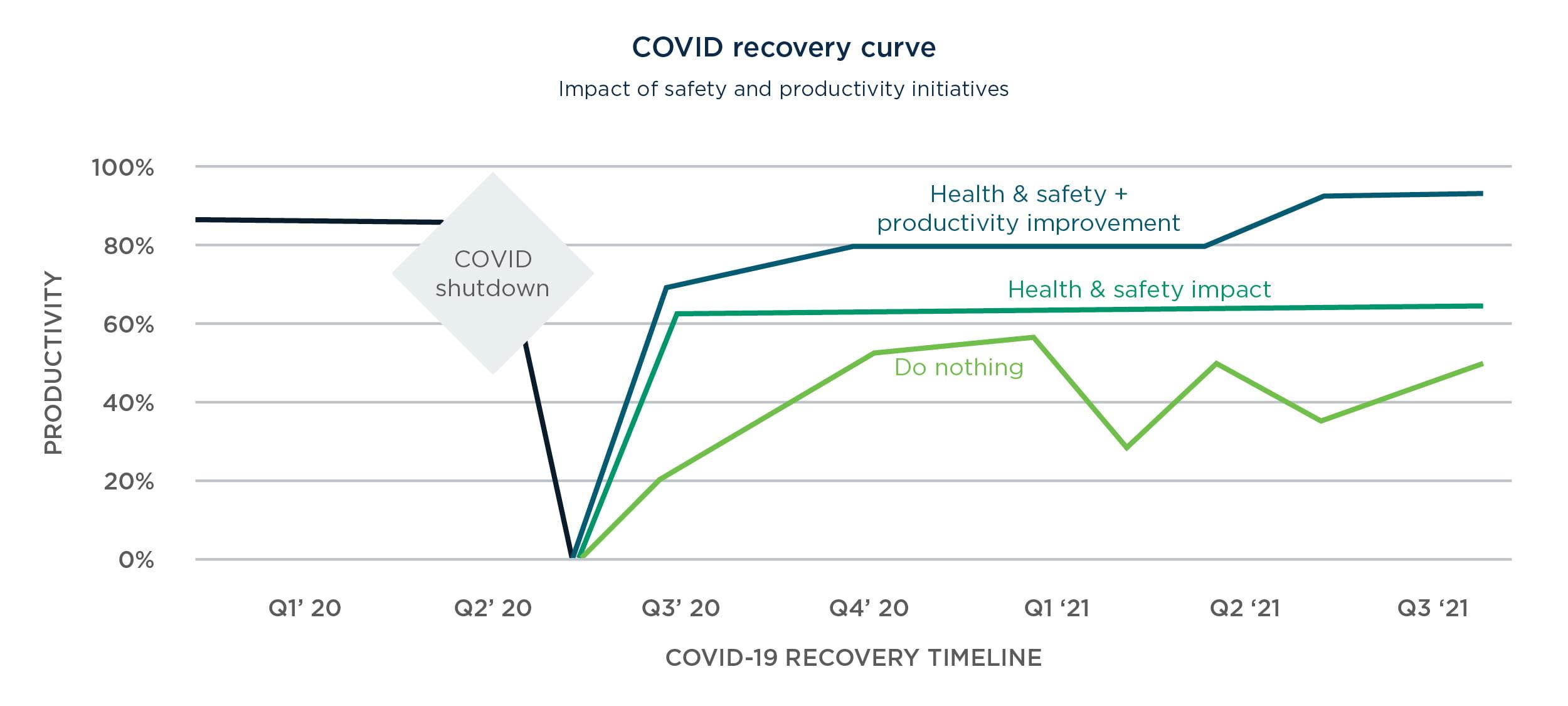
Prioritize the Health and Safety of Employees and Customers
The starting point for companies is to assure the health and safety of employees and customers – whether it be within the four walls of an office, factory, and warehouse, or in the field serving customers. All elements of an operational footprint must be considered to identify these risks. While there are several ways to identify and sort these considerations, we recommend following a standard people, process, and technology (PPT) framework.
People
- PPE requirements and availability
- Face-to-face supervisor engagement
- Employee distancing requirements
- Union work rules and limitations
- Personal health information (PHI) access
Process
- Cleaning and sanitation protocols
- Work cell and shop floor design
- Breakroom, restroom, common area protocols
- Standard operation procedures
- Daily operations/shift meetings
Technology
- Use of common kiosks, workstations, and time clocks
- Use of wearables to track employee health/contact tracing
- Use of automation and robotics
- Front line communications, monitors, and signs
- Use of remote controls, SCADA systems, among others
Essential Businesses are Leading the Way
Essential businesses have been adapting operations in real time while establishing new operational health and safety measures since the spread of COVID-19 halted the economy. Grocery, food, beverage, life sciences, and packaging industries are rewriting the workforce and workplace safety rule book.
While there have been some high-profile breakdowns, many essential businesses have rapidly developed and adopted new ways of working and can safely and effectively operate. As the economy begins to recover, businesses will be looking to the innovators among essential industries for insights and best practices.
The speed of recovery for businesses will be based on how essential their industry is and how ready and able they are to adopt new ways of working. The stronger their ability to innovate, adapt, and execute, the sharper their recovery trajectory will be.
Recovery Trajectory Matrix
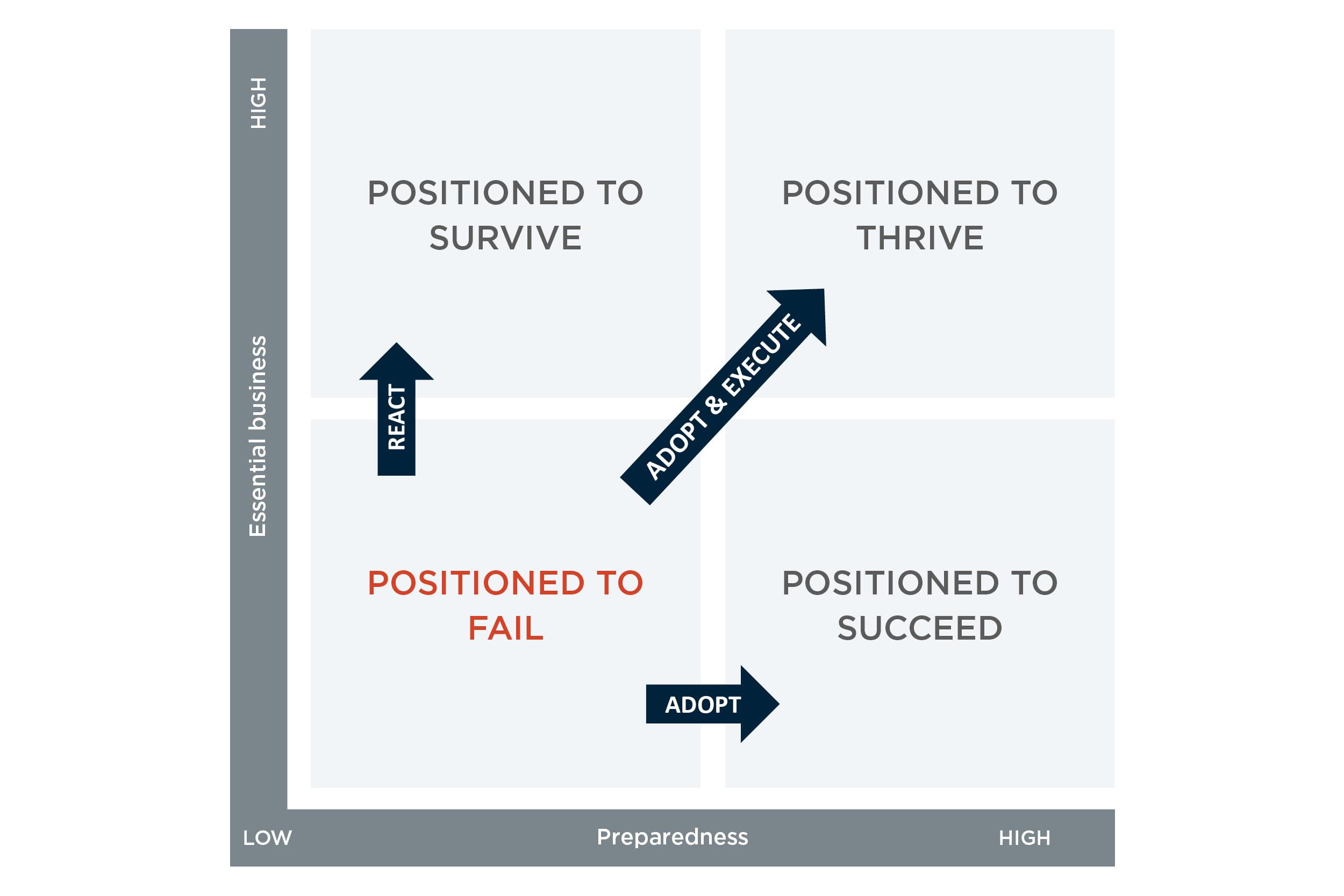
The Game Plan to Driving Safety and Productivity
As businesses recover, assuring the health and safety of their employees will be the top priority. Employees must feel secure at work and not fear exposing themselves or their families to any unnecessary infection. Once a safe work environment is established, companies need to shift their focus to adopting new ways of working that will improve productivity and service levels while also offsetting increases in operating costs due to the new health and safety protocols. We recommend a four-step approach to achieve this:
- Determine the safety risks and impact. Assess the health and safety risks across the operation to identify safety hot spots within facilities. Look across processes and procedures to flag interfaces and hand-off points among both employees and customers. Determine a fit-for-purpose cleaning and sanitation regimen and consider how technology is deployed throughout operations to provide safe access to workstations as needed. Once these have been identified and assessed, determine the impact that risk mitigation will have on performance.
- Identify and quantify productivity and cost improvements. Once the health and safety measures are defined and adopted, companies can then start to challenge historic operational capability to unlock new levels of productivity and performance. Employ classic Lean and industrial engineering principles to optimize processes, workflow, and facility designs. Accelerate digital strategies through expanding automation and robotic capabilities, deploy AR/VR and leverage AI-enabled, predictive models, all while maintaining a sustained focus on safety.
- Develop a safety and productivity recovery roadmap. Once actionable improvements are identified, prioritize these productivity and cost improvement initiatives based on impact, feasibility, and time to value. Develop a sequenced roadmap of projects that considers the organization’s ability to effectively adopt and sustain these new ways of working.
- Implement new ways of working. With the safety and productivity roadmap in hand, mobilize resources to pilot and expand the new ways of working. Support the improvements with a comprehensive change management and communication plan. Measure and report the results, share learnings and best practices, and celebrate successes through this significant transformation.
While no one can predict if or when the need for extensive workforce and workplace health and safety measures will ever be relaxed, the reality is there will be no temporary solutions nor short-term victories. To win the recovery game, companies will need to embrace sustainable safety measures while adapting and transforming the way they work to thrive.