Article
Building the factory of the future with a digital mindset
The factory of the future is near—but it requires a strong foundation with a digital focus
February 24, 2022
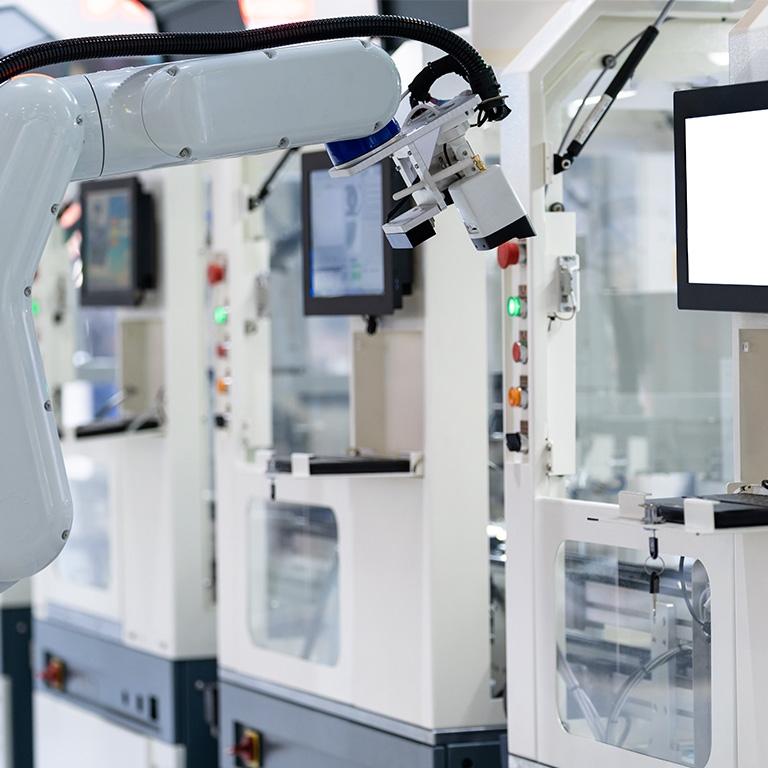
This article was originally featured in February 2022 issue of the Manufacturing Leadership Journal. ©2022 Manufacturing Leadership Council, a division of the National Association of Manufacturers. All Rights Reserved.
Mention “factory of the future” and some people conjure up visions of artificial intelligence, machine learning, and a lights-out facility. But a dark factory is far from how most manufacturers are thinking about their future—at least for now. In a recent Manufacturing Leadership Council study, only 3% of respondents saw this as the eventual state of their factory model.
From our perspective, there are three primary drivers behind the movement toward a factory of the future. One is around productivity and efficiency. Shop floors were once considered cost centers. But today, rich operational data is driving material transformation, making the shop floor the center of value creation. Data is helping manufacturers optimize parameters and production runs, configurations, schedules, and maintenance—thereby minimizing costs and maximizing value.
A second driver is risk reduction, using machine data to reduce safety, compliance, and other risks. The third is agility through a connected-worker environment—specifically, the ability to get information and signals to operators quickly so that they can work faster, safer, and smarter. This is particularly important as operational complexity grows due to proliferating SKUs, greater variability, and more frequent changeups.
Evolving technology is key to achieving these goals. As a result, planning for the factory of the future often centers on the technology: What will it look like? What is the roadmap? And what new technologies will help us get us there? That exercise is ultimately necessary and valuable. But having the latest technology will not produce the desired results unless certain fundamentals are in place.
Before you can be digital, you need the right foundation for a new operating model.
This isn’t the exciting part of building the factory of the future. In fact, it’s likely harder work than simply implementing technology. We see three focus areas that must be in place for the factory of the future: an operations data foundation, a cyber-aware culture, and—most importantly—people who are connected and equipped to make the most of technology. Each of these areas will affect how value is created.
Begin managing your data like an enterprise asset
Most manufacturers view the value of their data in terms of its use in optimizing operations. In the Manufacturing Leadership Council’s study on M4.0 data, 54% of participants said they measure the value of data in terms of its impact on operational performance and ability to drive value by managing cost of goods sold; maximizing on-time in-full (OTIF); increasing capacity and productivity in light of labor and material shortages; or improving efficiency and quality.
In that study, more than a quarter of companies surveyed said their manufacturing data volumes doubled or tripled in size over the previous two years. But in our experience, few companies are properly equipped to manage and use the ever-growing volume of data from their factory equipment, sensors, and assets.
To be able to automate or data-enable operations amid this environment and realize the results you expect, you need to have a clear handle on the data being generated and be able to manage how it flows between and among assets and systems. The only way to do that is to get in the trenches to identify, map, and document equipment/assets and data flow and put this information into a relevant management system.
For example, if the goal is to enable predictive maintenance, key steps may include:
Mapping asset ID and attributes—for example: location, installation, source system, responsible data manager
Creating and mapping the hierarchy of assets and subunits related to them
Defining asset, subunit, and instrumentation relationships
Determining the systems and processes needed to deliver data in the right level of detail for analysis of the root causes of equipment failures
Determining when and how maintenance records are captured and utilized and which systems and processes must be enhanced to provide a statistical basis for preventative maintenance
We see few manufacturers making this effort. Most understand the potential value but also the cost associated with it. If margins are tight, this can be difficult to justify. But if you don’t do this, how do you expect to be able to connect, secure, enhance, and realize value from new technology—let alone the technology you already have? What’s more, if you don’t address this early in the journey to digital operations, the effort required will only become more complex and costly.
Managing operations data is not only a critical steppingstone in the journey toward the factory of the future. It is also a prerequisite for monetizing manufacturing data—and delivering benefits that are potentially far more valuable than increased operational agility or efficiency.
Create a culture of cybersecurity
Security is a well-trodden topic in discussions about the connected factory of the future. Nevertheless, most organizations believe they still have work to do. In the Manufacturing Leadership Council’s research, more than half of the respondents (52%) assessed their company’s technical security level against potential cyberattacks or disruptions to plant floor systems/assets as partially secure. Only 26% consider their organizations to be totally secure. It is also a top concern of the C-suite: In our third quarter (2021) executive poll, cyberattacks represented the second-largest threat to conducting business, behind only hiring and retention of the workforce.
It’s hard to create confidence in a rapidly evolving risk environment. Most of the risks in manufacturing today involve ransomware. According to a Dragos and IBM Security X-Force report, ransomware attacks on industrial entities increased more than 500% since 2018, with manufacturing comprising nearly a third of ransomware attacks on industrial entities.
The impact can be greater than you think. Where the risks to manufacturing risks used to be beyond the shop floor—e.g., interrupting distribution—today’s shop floor systems increasingly rely on corporate infrastructure for connectivity and interconnection. That means attacks can stop the ability to produce as well as ship product. Consider an example where the images (intellectual property) printed on product are stored in corporate files. A ransomware attack prevents access to those image files for a period of time, thus stopping production. And if those images are the property of a co-manufacturer or customer, then a breach could open exposure to lawsuits.
Given the complexity, you will need a multi-faceted approach that focuses not just on monitoring but on cultural and behavioral change to mitigate risks. These are some key steps:
Bolster disaster recovery and continuity plans to ensure resilience in the network
This is important for any organization but especially now in manufacturing. Consider questions such as these and develop meaningful strategies around them:
- What is the worst-case scenario? How can we prevent that from happening? And how will we operate if it happens?
- How quickly can we isolate the manufacturing environment from the corporate network to maintain production while systems are recovered?
- What can we be doing to monitor the environment more effectively?
Address cybersecurity as early in the process of introducing new technology as possible
Rolling out new technology typically requires some retrofitting. Retrofitting is harder and comes at a cost—thus, it requires a business case. But security is about loss risk rather than return, so it is often an afterthought. Throwing on the controls at the end of the process can increase risk.
Embed it in the capital investment/management process
Better yet, make the approval process for investments in new technology contingent on proper up-front cybersecurity planning. This include establishing cyber procedures and frameworks and making sure what is on the floor is compliant with broader cybersecurity protocols.
Strive for a cyber-aware culture
Manufacturing tends to have an improvise-adapt-overcome mentality. Resourcefulness can be a good thing. But in today’s connected environment, it can also increase risk. Consider this example: The plant floor cannot connect to the corporate network, so someone attaches a router to fix the connectivity issue. However, that unprotected access point opens up the potential for a cyberattack.
A cyber-aware mindset is essential at all levels—starting with leadership. We have found it helpful to lead executives in a tabletop exercise that illustrates the impact of a lack of proper controls and the need to embrace a more robust security program.
At the other end of the spectrum, employees need to understand both the what and the why. You can have great policies around cybersecurity, but if people on the plant floor aren’t properly trained on basics as simple as email activity, they open the door to phishing or worse. In the example above, greater awareness may have prevented the employee from improvising by installing a router in a vulnerable location.
Consider taking the same approach to cyber as you have with safety—creating daily dialog around incidents and best practices, embedding cyber discussion into all meetings, and tracking and reporting cyber statistics specific to sites and the company.
Increase cybersecurity skills and capabilities within your operations
You can have a monitoring service look for incidents, but you cannot outsource the cybersecurity strategy and architecture — so you will need to find ways to build these capabilities internally. There is a massive shortage of cybersecurity talent in the market. The talent that does exist can command compensation many manufacturers—particularly mid-sized—cannot provide. Think critically about how you will upskill your IT and OT teams.
Make the connection between cybersecurity and safety
Manufacturers are hyperaware of safety and spend a lot of time and money to address OSHA requirements. Increasingly, cybersecurity incidents can cause different types of safety issues. For example, think about the risks in an auto factory with autonomous vehicles delivering parts or an IIoT-controlled saw that could turn on when someone is changing the saw blade. Understanding the safety risks of a connected factory helps build stronger awareness around security.
Empower the people who will run the factory of the future
Lastly, but most importantly, recognize that you can’t achieve operational goals with technology alone. The rubber meets the road with the people who use it. Whether you are talking about industrial IoT analytics or just simple management operations systems, unless you prepare people to use technology responsibly, you are opening doors to security, efficiency, safety, or other issues.
The factory of the future may employ more technology, but it is still about people. You need the right leaders, people, culture, and incentives to promote the right behaviors. In the Manufacturing Leadership Council’s research, a lack of skilled employees and organizational structure or culture that resists change ranked as two of the top four obstacles to transformation—higher than cybersecurity. Yet almost half of companies are still defining their M4.0 change management processes. Only 9% of those surveyed have a formal change management and training program in place for all plant floor employees, and over a quarter (26%) plan to but have not yet addressed change management.
Don’t underestimate the effort involved in driving the behaviors that will define the next decade. The current labor market only makes the challenge harder.
You will also need a purposeful approach and long-term commitment to creating a culture of adaptability, self-improvement, and change—and winning the hearts and minds of everyone in the organization, from top to bottom. Following are several ideas that we have found to be effective in driving the culture-related side of the factory of the future.
Be clear about what’s in it for the worker
Emphasizing a role’s value helps people see the big picture—why their skills are important and how elevating their skills can increase their value to the company. This can also help rebrand traditional manufacturing roles to appeal more to young talent, removing some of the stigma around repetitive work.
Refine your training
For many organizations, training — which may already have been limited or informal—took a backseat during the pandemic, so this is a good time to rethink your approach. Manufacturing training, particularly in factories, tends to focus on the what or how (do this but not this) but not the why. In an increasingly automated environment, teaching employees to think and understand is important for both safety and efficiency.
Additionally, managerial training has been a common void. In West Monroe’s study of managerial effectiveness, 59% of managers overseeing one to two other people received no training at all and 42% resorted to mimicking the managerial style of a former boss.
Consider new training techniques, such as new job aids or simulations. One idea that is easy to implement is building digital work instructions into new technology, creating an interface that shows operators every step of the process, with the specifications needed to make the product. This can also aid agility, making it easier for employees to move between roles as needed.
Personalize training
As roles become more specialized, training must become more tailored to individuals, with personalized plans and training timed for when people need to begin using new skills. For example, a younger operator with strong technical or analytical acumen won’t have the same level of experience with the machines to know when they will break or the manufacturing mindset to understand the data to be collected and analyzed. That person’s training plan should focus more on learning the operations. On the other hand, an experienced operator will need more emphasis on reading the screen, understanding the data it is presenting, and then using that data to make decisions.
Provide incentives
Many manufacturers provide a pay incentive for training—for example, an extra $0.25 per hour for meeting a certain skill criterion. If you do this, make sure you get a return on your investment by ensuring employees are staffed properly and are applying what they learned. Many organizations do not follow up adequately.
Redesign the employee experience
Introducing new technology provides an excellent opportunity to consider and purposely redesign the employee experience — ideally before introducing new tools and processes. This can facilitate both adoption and morale. But despite the growing prevalence of technology in the manufacturing workplace, this practice is not commonplace. In West Monroe’s research, 84% of companies said they sometimes or never redesign the employee journey before introducing new technology.
Measure the impact
Change management takes time and commitment. Typical manufacturing margins will make it difficult to make the business case for investments in training and change, so it is important to have metrics—from adoption to increases in efficiency or productivity—in place that illustrate the impact.
Conclusion
To begin progressing toward the factory of the future, most manufacturers need to start with the mundane—automating tasks such as collecting shop floor data for real-time monitoring and digitizing standard operating procedures — that provide a better line of sight so operators can make informed decisions, before setting sights on things like artificial intelligence, machine learning, or the lights-out factory. This is especially important in today’s revolving-door labor market, where the simpler and more straightforward it is to execute work, the easier it will be to integrate new workers into your operations.
No matter how grand or pragmatic the technology and digital vision, it will be impossible to derive full benefit if you don’t master several key basics first, including data management, cybersecurity, and the human side of change. Once you have a good handle on these, then you can begin digitizing the elements that make sense.